It typically occurs while you install a shelf or hang a door. You’re performing a balance act as you hold one component, hold another piece steady, and try to drive a screw at the same time. The connection pulls tight and the screw snaps when you tighten it on the last few threads.
I was interested to learn why some screws shatter while others do not. I’m confident that what I found will wow you as it did me.
Screw Fabrication
A screw’s strength is influenced by how it is made, which is intriguing. Bulky material is passed through a succession of shaping stations that stretch the stock to the required diameter. Some manufacturers supply steel stock that is ready to be manufactured into screws, while others supply stock that needs to be pulled and thinned to the proper size.
Once the material has been sized, it is sent through a machine that pounds the stock once to create the screw’s head and a second (or third, depending on the material) to create the recess, which is where the screwdriver goes to insert the screw. According to what I’ve heard, this technique shakes the facility floor with each pound.
Head Designs
There are many different types of screwheads, but the flat head—whose top is flush with the surface when the screw is properly seated—is the one that is most frequently used in woodworking. Additional head shapes include:
- Trim head: These resemble flat heads but have a flat surface with a reduced diameter.
- Oval head: Although the surface of these screws is countersunk, it has a somewhat elliptical form.
- Pan head: A flat surface beneath the dome-shaped head that serves as the bearing surface and remains above the surface of the wood.
- Truss head screws have a lower head profile and a somewhat bigger bearing surface than pan head screws.
- Washer head: This screw, used in cabinetry to mount wall cabinets, has an even greater bearing surface.
There are a few other designs that are occasionally discovered.
The countersink is the beveled section immediately below the head. On American screws, the countersink typically has an angle between 80o and 82o. The majority of commercially available countersink pieces fit that angle. Once more, you occasionally discover screws being made at different angles.
Recess Design
Although there are many different varieties of recess screws available, I’ve discovered that woodworkers typically employ three basic designs.
The first screw recess was the slot head. For the most, if not all, of my projects, I pick slot-head screws. I make that choice in an effort to stick to my mission of making replica furniture. Because it’s challenging to maintain the screwdriver’s engagement with the screw recess while a lot of torque is being applied to drive the screws, use of this kind of recesses has decreased with time.
Henry Phillips didn’t patent the Phillips recess until 1936. This recess, sometimes known as “cross-drive,” is still widely used in the American woodworking sector. When compared to slot screws, the ability to retain contact between the screwdriver and the Phillips screw recess is significantly improved. About 12 foot-pounds of pressure are used to maintain the driver’s engagement during a Phillips recess. If a carpenter is not concerned with obtaining a true, antique look, they will typically adopt this recess style.
The Phillips recess introduced a new issue known as “cam-out,” which happens when the recess is damaged by the screwdriver as a result of an excessive amount of torque produced while driving a screw, while the slot head allowed the driver to slip leading to damage to the screw’s head.
The square drive is the third screw recess seen in many woodworking businesses. Cam-out may be completely or significantly reduced thanks to this design. When driving a square-drive screw, you only need to apply 4 foot pounds of pressure to the driver to maintain it in contact with the recess. Consequently, the likelihood of the driver slipping is reduced.
I assemble shop fixtures and jigs using square-drive screws. Why? I tried a deck screw since I was having issues with screws breaking and wanted to see if there was a difference. I chose square-drive screws for the job. There was a distinction, but as I later discovered, it wasn’t because of the recess. The difference was in the screws.
Thread Styles
Screws are lengthened after the head and cavity have been produced, and then the threads are added. In the past, screws’ shanks were chopped to create threads, leaving the threads’ outer diameter at the same size as the shank (a great method for dating screws pulled from older furniture). The shanks are now pressed with threads. As a result, the thread profile is longer than the shank’s diameter.
Put your hands in a prayer posture and slide your right hand back until the tips of your fingers are at the palm of your left hand to demonstrate how threads are added to screws. In this illustration, the screw is held in the left hand, while the thread-cutting tool is held in the right hand, apply pressure with your right hand and slide it forward across your left hand.
A “single lead,” or a single parallel thread, wrapped around the length of the screw, has traditionally been the thread design for wood screws. The most popular thread style for woodworking screws is still this one.
Deep-thread screws were invented as a result of the use of particleboard in the furniture industry (isn’t that a lovely thought). The shank of this thread pattern is narrower, and the deeper threads are angled more acutely. Deep-thread screws are supposed to drive with less splitting, bursting, or material displacement and to retain better in composite woods.
Another type of thread design is “double lead,” in which two parallel threads that start at the screw’s point circle the shank. More threads per inch are produced by the double-lead thread design. Therefore, screws drive more quickly. However, screws longer than 3-12′′ in length typically have double-lead threads. The screw is stabilized by the double lead throughout the heat-treating process, which lessens the screw’s propensity to bend.
Heat Treating ProcedureScrews undergo a heat-treating procedure once the threads have been produced. The most crucial step in creating strong or weak screws is heat treatment. The components of the raw materials used to make the screws are another factor that boosts strength.
There are numerous ways to heat treat materials. The ideal approach is to divide the screws into more manageable amounts, like hoppers, and then put the screws through the procedure. With this technique, each screw is correctly heat-treated and may move more uniformly. Some producers shake the conveyor belt as the screws move along to further boost efficiency. The screws can mix and heat more uniformly when shaken.
Depending on the length of the screw being heat-treated, the temperature varies significantly, but on average, the furnace temperature is close to 1,600° Fahrenheit. The screws become more brittle at temperatures much above 1,600oF. They often break when driven if they are overly brittle.
When Heat Treating is Not Done
On some screws, heat-treating is not done. Some manufacturers exclude from the process one of the most crucial processes needed to increase the strength of screws. The major cause of why some screws break and others do not is this.
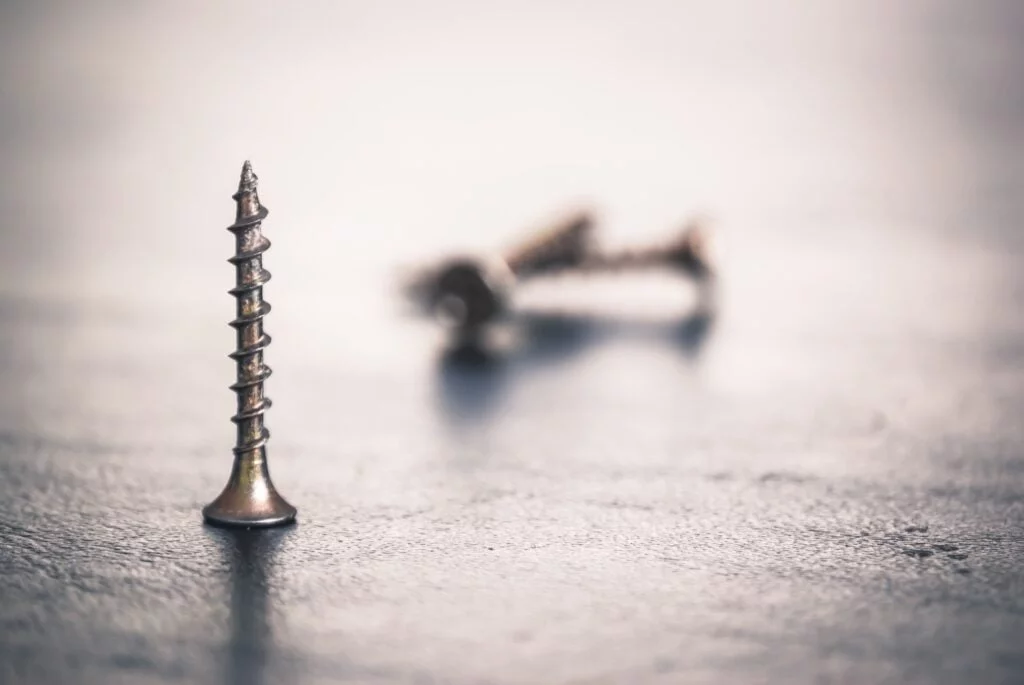
Drywall Screws
The characteristics that have been addressed thus far apply to wood screws. For a variety of reasons, drywall screws should not be used in woodworking projects, despite what you may have read or heard.
In addition to having a smooth "bugle head," or a curved transition between the shank and head, drywall screws also have a higher heat treatment temperature and are brittle. In addition, the countersink of the drywall screw does not match the depression formed when using a standard countersink bit. This design is to prevent the screw head from breaking the paper of drywall wallboard, which is the only true purpose for drywall screws.
Additionally, drywall screws typically feature big heads that are the size of a #8 wood screw and thin shanks that are the same size as a #6 wood screw. The large head reduces tearing through the paper face of the drywall as well.
It makes sense that a screw with those properties would be more likely to shatter when pushed into wood if it were tightened. The bugle-head design doesn't suit the countersink, and before the larger head is firmly seated, the slender shank approaches a point of tension.
To see other material construction, please see here.
To know other construction guides, tips, and methodology for beginners, veterans, and contractors, please see here.