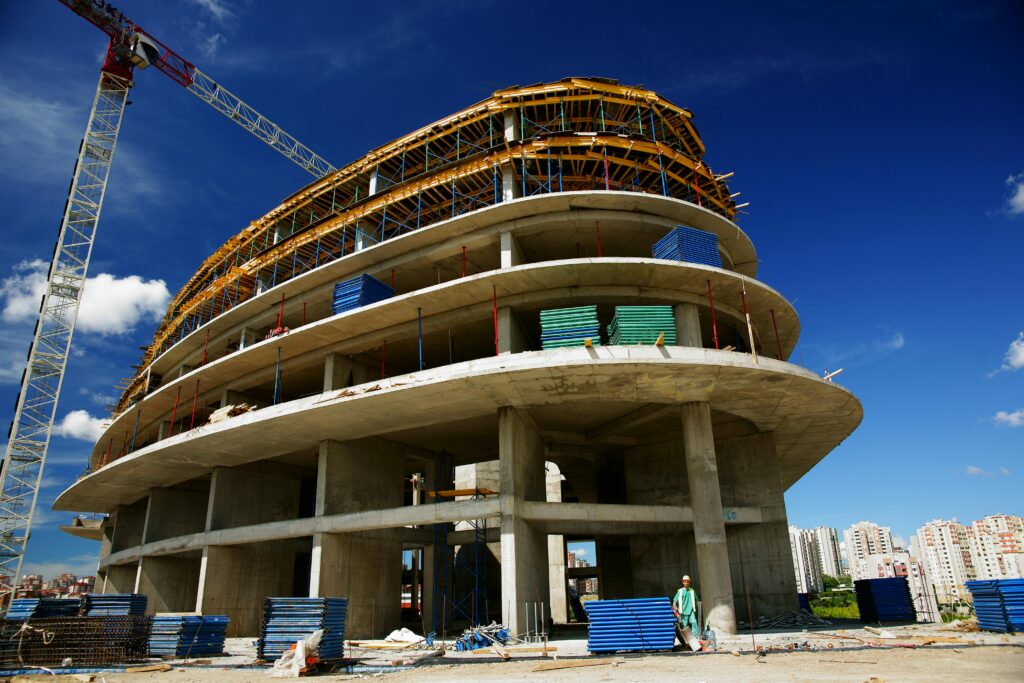
Simple Construction: One of the Best Procurement Procedures
In the construction industry, effective material procurement is essential to the successful completion of projects.
The procurement process involves a number of tasks, such as finding, acquiring, and managing the materials required for building projects.
Nonetheless, the intricacies involved frequently provide difficulties that may affect project budgets, schedules, and general quality.
This article delves into the complexities of construction procurement, examining how to improve project outcomes and expedite the procedure.
Understanding Construction Procurement
In the construction industry, procurement refers to the acquisition of different supplies, machinery, and services needed to complete a project.
These materials include anything from specialty tools and fittings to raw materials like steel and concrete.
Normally, the procurement procedure starts in the project planning stage and lasts through the phases of design, construction, and project closeout.
Key Components of Construction Procurement:
Sourcing: Finding trustworthy manufacturers and suppliers is essential to getting high-quality goods at reasonable costs. This entails investigating possible suppliers, evaluating their qualifications, and building connections that will allow for long-term collaborations.
Purchasing: After suppliers are chosen, the buying process entails contract negotiations, purchase orders, and delivery schedule coordination. To prevent miscommunications and conflicts, precise documentation and clear communication are crucial.
Logistics: Organizing logistics is essential to guaranteeing that supplies reach the building site on schedule. To reduce delays and overspending, this entails scheduling transportation, monitoring shipments, and maximizing inventory levels.
Quality Control: The success of building projects depends critically on the quality of the materials used. By putting strict quality control procedures in place, project integrity and stakeholder satisfaction are protected from errors, rework, and safety risks.
Challenges in Construction Procurement
Despite its importance, construction procurement is fraught with challenges that can impede project progress and outcomes:
Fragmented Supply Chain: A fragmented supply chain is a result of the many stakeholders that are frequently involved in the building sector. Communication breakdowns and inefficiencies can occur when architects, contractors, subcontractors, and suppliers coordinate.
Cost Overruns: These can put a burden on project budgets and profitability. They can be caused by fluctuating material prices, unforeseen delays, and inadequate planning.
Problems with quality: Poor quality control procedures can allow inferior materials to enter the building process, which can cause delays, rework, and impaired structural integrity.
Legal and Regulatory Compliance: Complying with legal and regulatory regulations makes the building procurement process even more complicated. Penalties, legal action, and reputational harm may arise from breaking restrictions.
Strategies for Streamlining Procurement Processes
To address these challenges and optimize construction procurement, stakeholders can implement the following strategies:
Integrated Project Delivery (IPD): By enlisting the cooperation of all project stakeholders early on, an integrated strategy can be adopted that can increase project efficiency, reduce conflict, and improve communication.
Technology Adoption: Using digital tools like automated inventory systems, Building Information Modeling (BIM), and procurement management software can improve visibility, expedite the procurement process, and support data-driven decision-making.
Supplier Relationship Management: You can obtain exclusive prices, dependable delivery dates, and access to cutting-edge goods and services by building solid relationships with your suppliers through mutual respect, open communication, and trust.
Risk management: Reducing interruptions and guaranteeing project continuity can be achieved by putting strong risk management techniques into place to recognize, evaluate, and reduce procurement risks.
Continuous Improvement: You can promote continuous improvement by routinely reviewing your procurement procedures, getting input from stakeholders, and putting what you’ve learned into practice.
Case Study: Modular Construction
Innovative modular construction offers special chances to expedite procurement procedures by assembling prefabricated building components off-site.
Modular construction saves waste, expedites construction, and decreases procurement complexity by standardizing designs and supplies.

Conclusion
The success of building projects depends on the efficient purchase of materials.
Through comprehension of the intricacies involved, resolution of obstacles, and application of efficient procedures and optimal techniques, interested parties can maximize procurement results, improve project efficiency, and attain higher levels of success in the ever-changing construction sector.
To see other material construction, please see here.
To know other construction guides, tips, and methodology for beginners, veterans, and contractors, please see here.