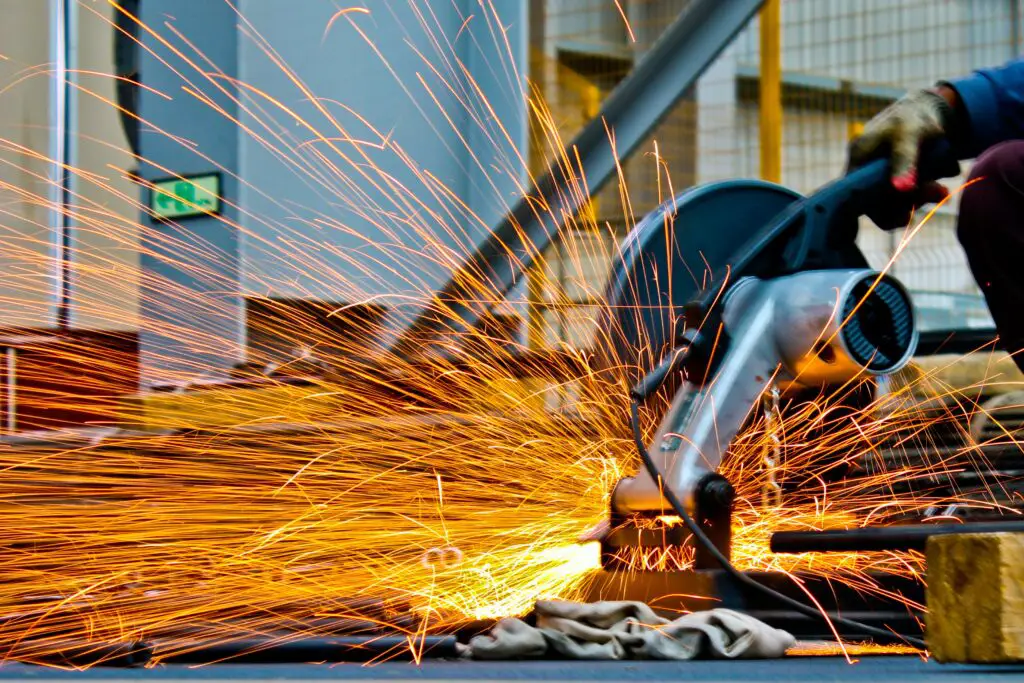
What is “Cold Rolling” Stainless Steel? And is it Guaranteed Good?
Stainless steel is frequently processed via cold rolling, a work-hardening method that modifies the structure of metals. There are numerous uses for cold-rolled stainless steel as a raw material in the fields of medical, aeronautical, and automotive engineering. Continue reading to find out more about cold rolled steel, including what it is, how it is made, and what it may be used for.
What is Cold Rolled Stainless Steel?
Cold rolled steel, often known as CRS, is a well-known material that is incredibly ductile and works well in applications where accuracy is required. It is utilized in numerous products, including furniture, filing cabinets, lockers, and home appliances. CRS is frequently used in construction applications to construct garages, steel sheds, and other industrial structures.
Simply put, cold rolling is the technique of shaping steel without the use of heat in order to strengthen it. In contrast to hot rolling, which is used to make hot rolled steel, cold rolling can only take place when a metal is below its re-crystallization temperature. Cold rolling is done at room temperature, as opposed to hot rolling, which is done at high temperatures. Mechanical stress is utilized to alter the structure of metal instead of heat. The strength of the metal can then be increased by up to 20% through strain hardening, which can also enhance the metal’s surface quality.
When metal is mechanically stressed during the cold rolling process, it permanently alters the metal’s crystalline structure. Its strength is increased as a result, and corrosion resistance frequently gets better. Better dimensional accuracy is another benefit of cold rolling in addition to enhancing surface polish.
Precision manufacturing is possible while creating a cold rolled stainless steel coil, which enables the production of the metal to exceedingly tight tolerances. Cold rolling is a method of work hardening stainless steel that enables us to produce several degrees of temper, including quarter, half, and full hard. How much cold work has been done on the steel determines how hard it is. Hard stocks that are quarter, half, and full have bigger reductions (occasionally up to 50%). This raises the yield point while lowering the steel’s ductility. Steel that is just half as hard can be bent back over itself without breaking, while steel that is fully as hard can be bent at a 45-degree angle without breaking. When bending metal without the risk of it breaking, cold rolled metal is frequently employed.
The following are the several stainless steel grade families that are frequently cold rolled:
- Austenitic Stainless Steel
- Ferritic Stainless Steel
- Martensitic Stainless Steel
- Precipitation Hardening Stainless Steel
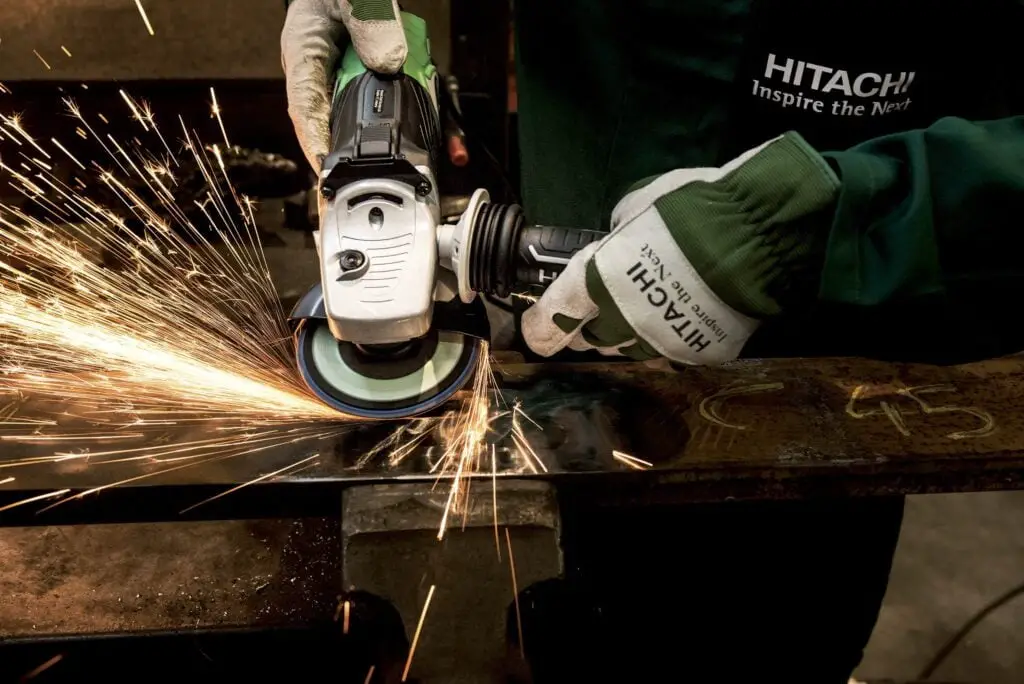
How Does a Cold Rolling Mill Work?
Sheet metal or strip coils are the first step in the cold rolling of a metal alloy. Large rollers are used to compress and squeeze these materials to a point just below their ultimate tensile strength. Different mechanical and hardness qualities are achieved in the completed product depending on the degree of compression. By processing steel strip through a series of tandem rolling mill stands, cold reduction can reduce the metal’s thickness. These stands have vertically stacked rolls that are propelled by huge motors. The motors exert a lot of effort to compress the metal extremely.
These mills thin out coils of hot-rolled, pickled goods by passing them through. The metal has finished rolling once it has gone through the rolls and reached the desired thickness, but it is still not quite ready for use. The metal is still heavily cold-worked at this stage of the process, and although it has a high strength, it can also be fragile. To soften the steel and make it easier to deal with, it must be annealed at a higher temperature. Because it can be bent and molded once the metal has been annealed, it is simpler to use it in many applications.
Another technique for cold rolling involves passing the strip back and forth between mandrels using a reversing mill. By doing this, the strip’s thickness is lowered with each pass until the desired thickness is achieved. Cold rolling can reduce metal by 60 to 80 percent, which can then be used to make consumer goods or for use in other industries.
Can Metals other than Steel Benefit from a Cold Rolling Mill?
Although steel is the material that is cold rolled the most, numerous other alloys and metals can also be cold rolled to alter their crystalline structure. Permanent flaws are produced when they are rolled at temperatures below their re-crystallization threshold. These flaws lessen the crystals’ mobility within the metal’s structure, increasing the metal’s tensile strength and hardness.
Cold rolling can be used on a variety of metals, including stainless steel, titanium, aluminum, and nickel alloys. Although cold rolling improves the strength and surface smoothness of metals like stainless steel coil, it also reduces the ductility. The same holds true for cold-drawn or rolled metal wire. But after being annealed, the metal is prepared for a variety of applications.
Cold Working Methods for Manufacturing
DEEP DRAW
A coiled coil is punched through a hole or die when deep drawing metal. The desired shape is created with the punch. The punch and die cavities are identical, however the bigger die cavity provides for clearance and passage. The compression force pushes the raw material into the die. Each draw operation is a separate step, and with each step the part’s height or depth increases as the part’s diameter decreases. This is done to make sure that re-crystallization also takes place as the metal changes shape. Battery enclosures, implantable medical devices, and aerospace and defense components for aircraft are among the products produced by deep drawing.
COLD EXTRUSION
Even though extrusion is still a relatively new metalworking method, it represents a significant and adaptable manufacturing process. Cold extrusion uses either ambient temperature or a slightly raised temperature to push a slug of material through a die. A product with a constant cross-section is the result of this. Tin, aluminum alloys, copper, lead, steel, and other metals can all be extruded.
PRECISION STAMPING
Another manufacturing method that works well for creating metal goods with precise tolerances is metal stamping. A flat metal strip coil is formed into a variety of shapes during the metal stamping process. Several various metal forming processes, including punching, coining, piercing, blanking, and bending, are used in this intricate process.
ROLL FORMING
In roll forming, a long strip of metal (often coiled steel) is bent by passing it between several sets of rolls, each of which completes a smaller portion of the bend. Until the desired cross-section profile is achieved, the finished product is bent.
As you can see, there are several applications for cold-rolled steel across a wide range of sectors. Contact one of Ulbrich’s metallurgical specialists if you have any questions concerning cold rolled metals. They can assist you in identifying the ideal alloy, grade, and qualities for your requirements. With almost a century of experience cold working metals, Ulbrich is pleased to serve customers in the nuclear, aerospace, and medical industries.
To see other material construction, please see here.
To know other construction guides, tips, and methodology for beginners, veterans, and contractors, please see here.