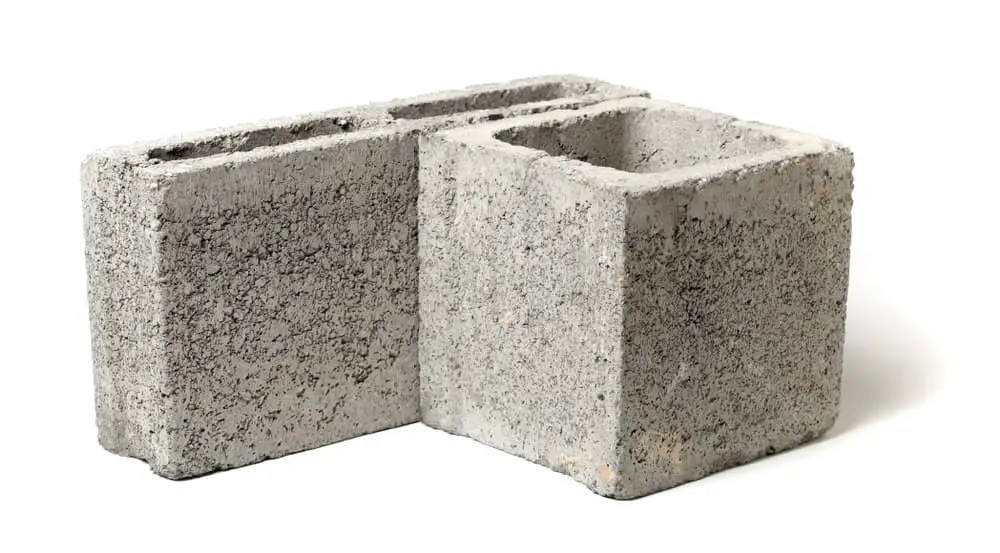
Simple Reasons Why Hollow Blocks are Highly Used in the Philippines
In the Philippines, Concrete Hollow Blocks (CHB) are one of the most often utilized walling materials. This is due, in part, to their relatively low cost as compared to other materials and the rapidity with which semi-skilled laborers can install them. CHB walls are extremely vulnerable to lateral loads (pushing or pulling forces from typhoon or earthquake). The CHBs’ resistance to lateral loads can be improved by adding steel reinforcing bars within on both a vertical and horizontal axis.
Typical applications in humanitarian shelter projects
between reinforced concrete columns and beams as a non-loadbearing filler (frames). In the Philippines, CHBs are frequently erected between reinforced concrete columns up to the window sill level, followed by the installation of lightweight walling materials, such as timber frame covered in amakan, plywood, or bamboo, above.
As a load-bearing filler material in constrained masonry constructions between reinforced concrete columns and beams. In order to increase their resistance to lateral stresses, the CHBs are strengthened with vertical and horizontal steel bars attached to the reinforced concrete columns and beams.
In reinforced masonry buildings as load-bearing reinforced CHB. In order to increase their resistance to lateral loads, the CHBs are strengthened with vertical and horizontal steel bars.
Advantages of using Hollow Blocks
- Readily accessible item
- Excellent thermal and acoustic resistance
- High resistance to fire
- Can be strengthened to provide more lateral protection from earthquakes and typhoons
- 20 years or more
Other Main Information About Hollow Blocks
Standard size of Hollow Blocks in the Philippines | Length – 40cm, Height – 20cm, Depth 10cm (4”) and 15 cm (6”) |
Product and material quality | For making CHBs, crushed coarse sand or gravel works well. Sea sand and sand from rivers should not be used. Between suppliers, there are major differences in the quality of CHBs. |
Suppliers | Sand and Gravel: Widely accessible from local vendors in the Visayas region. Cement: Identical to Above CHBs: Purchasing goods from companies whose goods have been approved by the Department of Trade and Industry (DTI) and Department of Public Works and Highways is advised (DPWH). To confirm that the cement satisfies the necessary requirements, look for the PS and ICC markings. |
Challenges | It can be challenging to get high-quality raw materials and CHBs locally. |
Environmental Considerations | Where possible, take into account more environmentally friendly options, like as interlocking compressed earth blocks (ICEB), as seen in this case study: http://www.rafi.org.ph/newshighlights/houses-bajaus |
Existing Standards for CHBs and CHB Wall construction in the Philippines:
Reference: National Building Code of the Philippines and National Structural Code of the Philippines, NSCP.
Load Bearing Walls | 6” CHBs CHBs used must be Type I Class A or B unit, confirming with ASTM C-90-70 |
Minimum Compressive Strength | 5.41 Mpa (800psi) – For individual CHBs 6.89Mpa (1000psi) – Based on the average gross area of 5 units |
Non-load Bearing Walls | 4” CHBs |
Steel Bars | 1 part Portland cement and 3 parts sand are to be used as the mortar (1:3) According to a structural engineer’s recommended vertical and horizontal spacing. |
Mortar and Grout | Type 1,2,3 or Type 4 Portland Cement confirming to ASTM C-150. Standard mix to the building code specifications |
Concrete Proportioning for the Production of CHBs
This is done in two different ways | By weight or volume. The most common method is by volume (e.g. using a bucket) |
Mixture | For CHBs: Mix Proportion 1:7, as per structural engineer’s specification |
Water | One should utilize pure water. not more than 28 litres per 40 kilograms Slump test results (per ASTM C-143) for each bag of cement must not exceed 10 centimeters, unless a structural engineer specifies otherwise. |
Common CHB Mix: | ½ bucket water 1 bucket cement 7 buckets sand |
Common Mortar Mix: | 1 bucket water 1 bucket cement 3 buckets sand |
Mixing Time | When using a batch mixer, employ precise timing and measuring tools to follow the manufacturer’s instructions when using. Ideally, revolutions would 14 to 20 times every minute. |
Curing | The CHBs should be covered with a covering after being taken out of the mold. for at least 7 days, covered with a damp tarpaulin or plastic sheet. in order to treat someone properly. You can accomplish this by consistently spraying. Keeping them submerged in tanks or covering them with water. a potent cure a procedure results in a stronger, harder, denser, and more enduring concrete |
CHB Tips
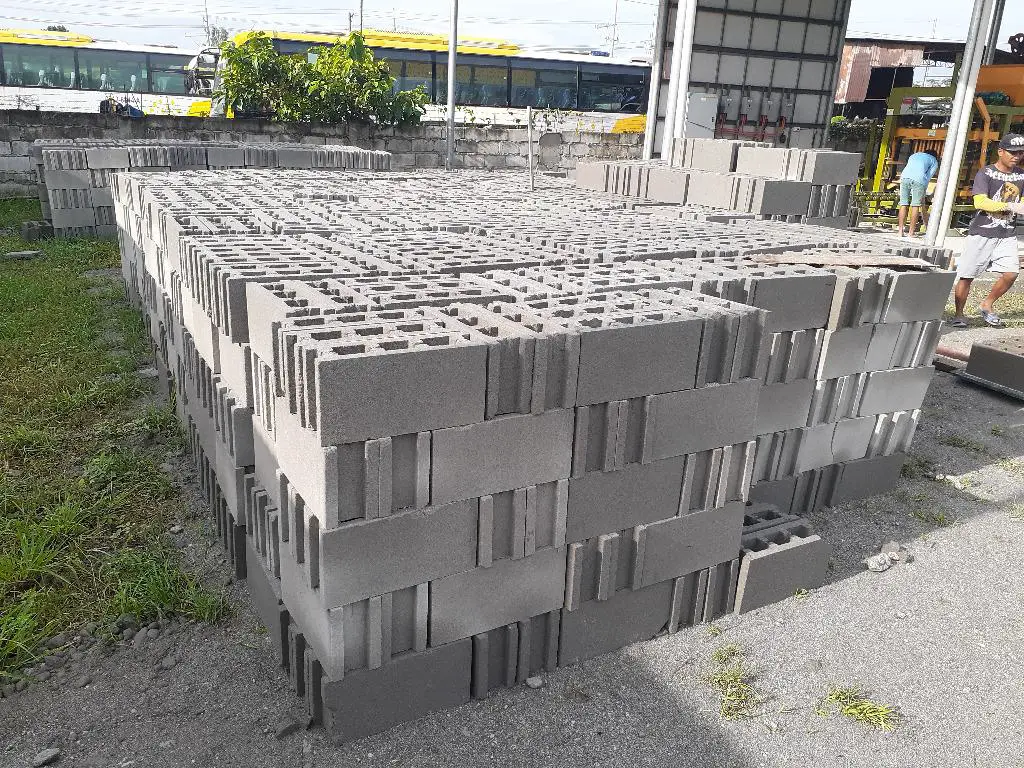
When choosing raw materials to make CHBs, it is advised to choose ingredients of high caliber and cleanliness. Beach sand should not be used as it contains salt, which greatly reduces the quality of concrete.
Material ratios in the mixture: Use the ratios recommended by a structural engineer to thoroughly mix concrete. Make sure to add enough cement, and stay away from using too much water, which may weaken the mixture. When mixed, concrete should stand upright and not run away from too much water.
Use a mixing board when blending; otherwise, the water will seep into the ground and the mixture may contain contaminants like dirt and grass. If concrete is mixed in batches, make sure that each batch has the same ratios.
Prior to pouring, make sure the formwork is clean and vibrate it uniformly. In order to ensure that any trapped air (weak spots) is removed, the concrete needs to be tightly compressed.
Because freshly manufactured, uncured CHBs are still experiencing shrinkage, avoid utilizing them.
Before utilizing CHBs, keep them in storage for at least 14 days after curing. Protect them from rain and ground water by stacking them so that air can move between and around them.
Reduce the amount of time CHBs are handled and transported to prevent damage.
It is advised to test the compressive strength of CHBs made or acquired to make sure they fulfill the necessary strength standards. Choose only robust CHBs. When handled, blocks with cracks and disintegrating corners indicate low quality. Avoid using it or any other blocks from the same batch if the CHB breaks when dropped from head height.
As dried brickwork collects water from the cement, weakening the joint, dampen CHBs before laying. Vertical joints must always be filled and a full mortar bed must always be used to lay down CHBs.
Connect CHB walls to the reinforced concrete columns and beams with vertical and horizontal steel reinforcing bars in accordance with the structural engineer’s specifications to strengthen the building’s resistance to lateral loads (pushing or pulling forces from a typhoon or earthquake).
Consider plastering or rendering the surface of CHB walls to prevent excessive moisture absorption and to make routine cleaning easier.
To see other material construction prices, please see here.
To know other construction guides, tips, and methodology for beginners, veterans, and contractors, please see here.
To know the flood prone areas in the Philippines, Top 10 Flood-Prone Areas to Live in the Philippines.