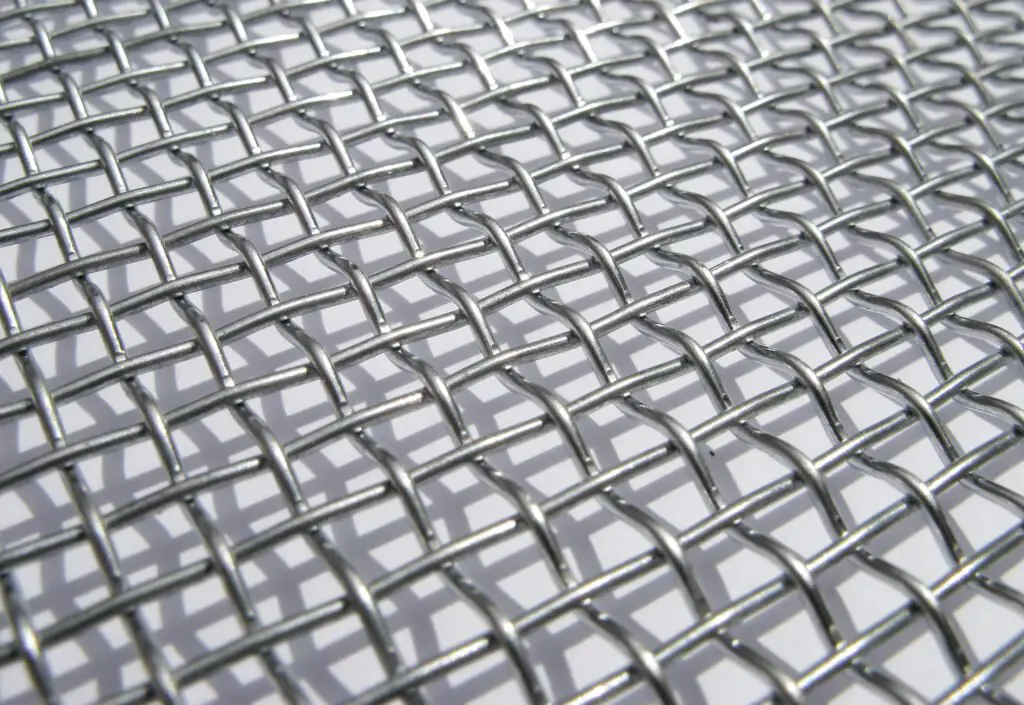
What is Wire Mesh? And What it is made of?
Wires of different thicknesses are intertwined, woven, or joined to form proportionally equal parallel rows and intersecting columns to form wire mesh. Wire mesh is made by weaving wire on commercial looms, leaving square or rectangular gaps between the wires. It is also known as wire fabric, wire cloth, or hardware mesh. Utilizing an electric welder, parallel longitudinal wires are joined where they intersect to create welded wire mesh or fabric.
The main purpose of wire mesh, which comes in an infinite variety of shapes, sizes, and configurations, is to separate, screen, structure, and shield numerous applications and processes. It is created from a variety of materials that are very durable and tough. Galvanized steel, stainless steel, aluminum, steel, and copper alloy wire are among the different types of wire. The kind of application, essential tensile strength, required flexibility, and preferred wire type and style are some of the criteria taken into consideration.
How Wire Mesh is Made
Wire mesh is created through the procedures of weaving and welding. Wire weaving is comparable to the process of weaving fabric on a loom, and welding is used to connect the wires where they meet. Automated machinery are used to finish both procedures.
Wire Weaving
The demand for woven wire cloth for the mining and pulp industries increased around the end of the 17th century, which sparked the creation of wire weaving looms. Wire mesh is now used in architecture, plastic extrusion, aggregate screening, and filtration processing in addition to mines and pulp mills. The current industrial wire weaving business was sparked by the increase in demand.
Weaving looms are used to create mesh rolls that are 48″, 60″, 72″, 98″, or even wider. The loom has a take-up mechanism, rapier for moving weft wire, reed, warp beam, and heddle frames.
Manufacturers weave meshes with predetermined and unique patterns on looms. Depending on the demands of the customer and their specifications, the finished mesh rolls are cut to a variety of lengths. Warp wires are those that are woven lengthwise or horizontally, and weft wires or shute wires, which are words frequently used in the textile industry, are those that are woven vertically or across.
Warp Beam are cylindrical drum covered in warp wires serves as the warp beam. To prevent the woven mesh from extending, the tension of the warp beam must be carefully regulated. The mesh width determines the number of warp wires, which must all have the same length.
Heddle frames are used to divide the wires that the warp beam feeds. The majority of looms have two heddle frames, one of which is used to raise half of the warp wires and the other to lower them. The weft wires cross the warp wires, shifting the location of the heddle frames.
At each cycle of the heddle frame, the rapier carries the weft wires across the entire width of the fabric. Between each set of warp wires, it feeds a single weft wire.
The reed maintains the warp wires’ proper alignment, spacing, and separation on the warp beam. The reed beats the weft wires tightly into place after the weft wire crosses the warp wires.
Take-Up is a pickup roller and two additional rollers that work together to wind the fabric to the cloth roller make up the take-up mechanism, which removes the fabric from the loom. The cloth is twisted in single layers, and after being run through the set of rollers, it is given a smooth, flat surface.
After the loom is put together and the warp beam is loaded, weaving is finished automatically. The warp beam unwinds gradually and uniformly as the loom runs. The take-up mechanism winds the woven finished cloth in parallel with the warp beam, feeding the warp wire at the same rate. The loom’s synchronous movement aids in keeping the warp wires taut.
Welded Wire Mesh
The intersections of the woven wires are welded together during a semi-automatic process to create wire mesh. The crossings at the horizontal and vertically aligned wires are programmed to be welded by welding equipment. The connections are joined using a variety of welding methods, including as resistance welding, tungsten inert gas (TIG) welding, plasma welding, and soldering.
Feeding wires into a weld mesh machine, which resembles the heddle frames and reeds used in wire weaving, is the first step in the process of welding wire mesh.
Spools of wire are passed one at a time through a straightener. Separately from the wires fed from the spools are inserted pre-cut wires that are the same size as the wire mesh. The wires are mechanically straightened to lay flat on the welding surface because they are fed from spools, whether they are pre-cut or fed from them.
Wires that have already been cut are positioned flat across wires that are being fed from spools. In mesh welding, the wires are perpendicular to one another at right angles.
Only bigger wires that can endure the welding process can be utilized to create welded mesh, which is heavier, more robust, and stronger than woven wire mesh. Because the wire is welded, it is more solid and long-lasting, which makes it perfect for concrete mesh sheets, cages, and fencing.
To know the pricelist of grout, Tile Grout Guaranteed Best Construction Material Philippines’ Prices
To know other construction guides, tips, and methodology for beginners, veterans, and contractors, please see here.
To know the flood prone areas in the Philippines, Top 10 Flood-Prone Areas to Live in the Philippines.
To know more about Concrete Hollow Blocks, Simple Reasons Why Hollow Blocks are Highly Used in the Philippines
To know more about Hammers and Nails, Tips for Guaranteed Best Technique for Hammering Nails
To know more about Tees and Wyes, What is the Guaranteed Best to Use: Sanitary Tee Vs Wye